The fast and the fabricated: Art lab manager designs a street-legal car
RESEARCH & INNOVATION
Studio art lab manager Nathan Hansen-Hilliard had what he called an “insane” project idea, spurred by a sleepless night. Up late and restless one night around five years ago, he came across kit car videos on YouTube.
Down the rabbit hole he went, watching people build lightweight street cars at home that resembled dune buggies. These gearheads were following kit car instructions, culling essential parts from used “donor” vehicles and connecting them with new parts from the kit.
“I have the capability to do much more than that here at the school,” Hansen-Hilliard remembered thinking. And make the car cooler-looking, too.
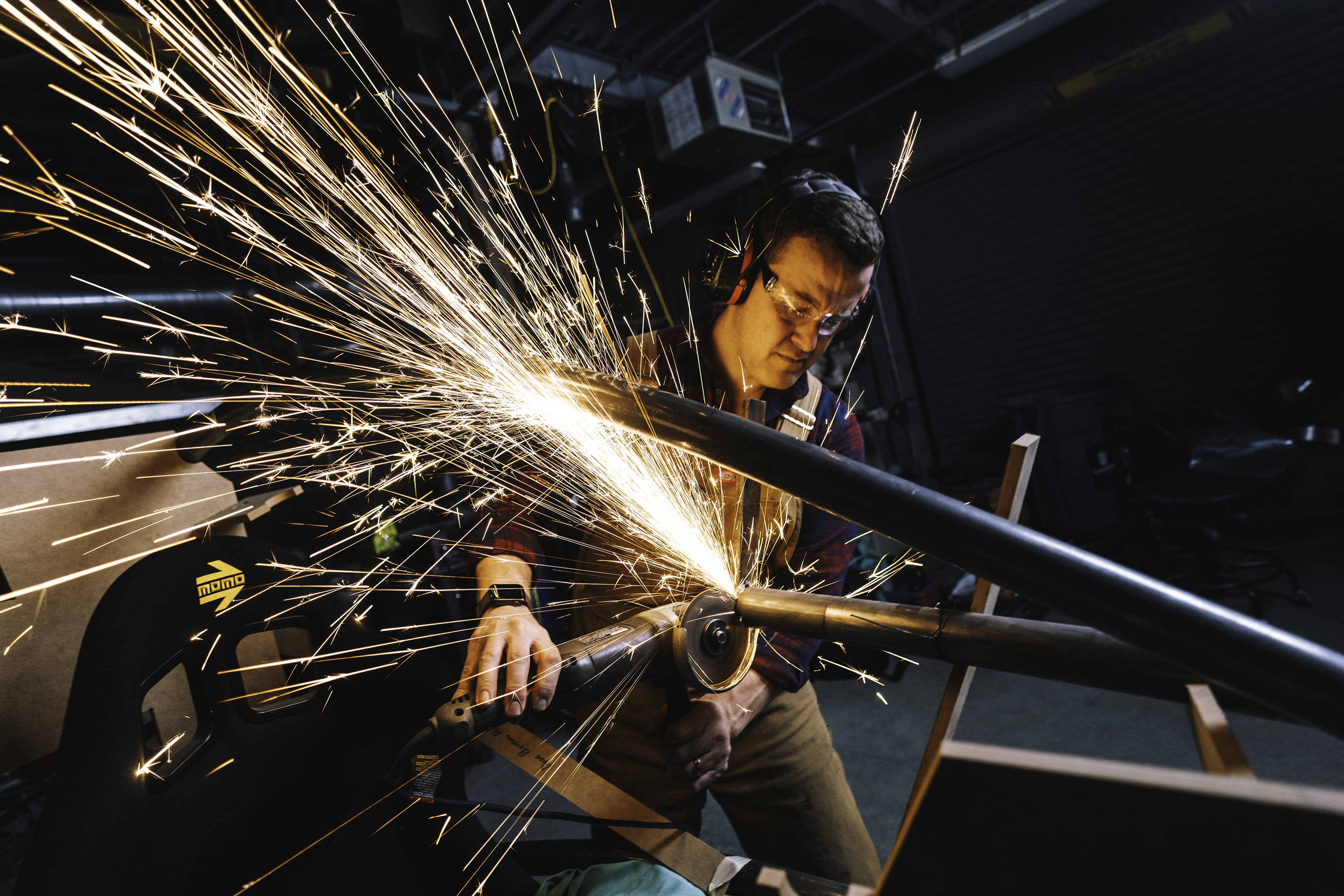
In that moment, he decided to design and build a fully functional vehicle from scratch at UR using art and art history department tools. No kit. Rather than the toy-like buggies in the videos, he pictured a Batmobile crossed with something from a Mad Max movie.
He faced a steep climb. “I could change oil, change a starter, and I can change a tire very well. That encompasses my entire knowledge about cars before I started this project,” he admitted. “But I enjoy making things that are difficult and offer me opportunities to learn.”
Originally from Texas, Hansen-Hilliard has a BFA in sculpture and an MFA in craft and material studies from Virginia Commonwealth University. Most of his artwork tends to be time-consuming, and a few pieces were literal clocks.
In his role at the University of Richmond, he’s responsible for managing health, safety, and smooth functionality in the art and art history department’s roughly 70,000 square feet of studio and lab spaces for painting, drawing, printmaking, and time-based media such as sculpture, audio and video, and photography.
“There is this romantic idea about artmaking,” Hansen-Hilliard said. “And it is fun, but a lot of our labs are like makerspaces in that they’re basically industrial environments.”
The visual and media arts practice program resources include computer numerical control (CNC) routers that automate control of machining tools for precision work, 3D printers, laser cutters, a plasma cutter for steel, and a full-blown fabrication shop.
Hansen-Hilliard drew design inspiration for his car from the British automaker Ariel Motor Company’s Nomad and Atom vehicles.
Last winter he bought a bright yellow 2006 Chevy Cobalt and methodically took the rusty used car apart, preserving the engine, wiring harness, and computer “brain.”
He’s purchased some parts such as tires, seats, seat belts, and brake lights. However, he’s creating nearly everything else himself. That means building the vehicle frame — or chassis — plus other elements like the muffler, the headlight housings as well as the parts that hold onto the wheels.
Relying on computer-aided design and manufacturing software to produce physical car components felt akin to operating a satellite in space for Hansen-Hilliard. He plugged instructions into CNC-type machines to transform digital models into a physical objects. Although he hasn’t used the 3D printer yet, he expects it will come in handy for printing small plastic pieces such as the headlight housing.
“I have indirectly learned how to do all these little things to make my life and project easier,” he said. “All of that gets translated to students as demonstrations or possible methods of making.”
Hansen-Hilliard's efforts received a boost from the Tribble Grant, established to support research projects within the department, especially those that directly benefit students.
Whenever a new machine arrives, Hansen-Hilliard learns how to operate it so that he can show others, making the tools more accessible. He did the same with a state-of-the-art 3D scanner. By scanning the engine and the chassis, he used digital modeling to figure out how to fit them together without needing to take esoteric measurements.
“You could start with something physical, scan it, alter it digitally, and print it out, and then alter it again,” he said. “It becomes much more of a circular opportunity for making.” He added that this might be a possible approach within sculpture classes.
By summer 2025, he’s hoping to drive the vehicle around the parking lot at UR.
To be clear, Hansen-Hilliard doesn’t consider his car to be artwork. He plans on making sure the vehicle will be street legal in Virginia, which means adjustments like installing airbags.
Recently his wild vision finally started taking shape.
"Three months ago, it looked like a maniac’s contraption,” Hansen-Hilliard reflected. “When people walk in now they say, ‘Oh who’s building the car?’”